Manutenção centrada em confiabilidade (MCC)
A manutenção centrada em confiabilidade (MCC) é uma estratégia em nível corporativo projetada para otimizar os programas de manutenção, estabelecendo níveis mínimos seguros de manutenção do sistema produtivo. O MCC enfatiza a combinação de ativos individuais com as técnicas de manutenção mais prováveis de fornecer resultados econômicos. A implementação bem-sucedida aumenta a confiabilidade e o tempo de atividade do equipamento, gerando economia para a empresa.
A MCC é uma estrutura completa que tenta sempre estender a vida útil do equipamento e diminuir o tempo de inatividade da maneira mais econômica possível. O objetivo principal do RCM é mais bem compreendido pela análise de suas palavras-raiz:
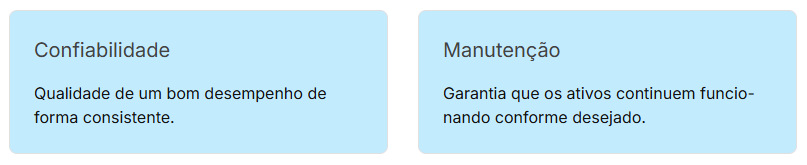
Essencialmente, a MCC fornece um roteiro para analisar e agir sobre as causas raiz das falhas do equipamento – tecnologia, cultura, projeto e ineficiências da estratégia de manutenção –, em busca de confiabilidade e para tornar os ativos acessíveis.
Obviamente, o tempo de inatividade não pode ser evitado ao trabalhar com máquinas complexas. No entanto, as organizações de primeira linha usam a MCC para evitar interrupções repentinas que exigem manutenção trabalhosa, terceirização cara e perda de tempo de produção.
A confiabilidade de um ativo é baseada na probabilidade de uma aplicação desempenhar sua função necessária em um determinado período. A probabilidade, por sua vez, certamente é um conceito estatístico expressado por:

Se a resposta for igual a 1, haverá, com certeza, a ocorrência do problema e o valor representado por 0 indicando a probabilidade nula de o evento acontecer.
Critérios de avaliação
Os líderes da organização devem delinear seus objetivos de MCC considerando a disponibilidade de gerenciamento, tecnologias acessíveis e recursos orçamentários. Esse processo um tanto demorado analisa cuidadosamente os cenários de ativos individuais antes de atribuir as tarefas de manutenção correspondentes.
Implementação
A melhor maneira de implementar um programa de MCC é adotar uma abordagem lógica e lidar com uma etapa de cada vez. Embora existam diferentes maneiras de implementar o MCC, essas sete etapas básicas são uma ótima forma para começar:
Etapa 1
Escolher um ativo no qual realizar a análise MCC. Que critérios devem ser usados para selecionar o ativo? Alguns fatores a serem considerados incluem o quão crítico o ativo é para as operações, seus custos de reparo no passado e seus custos anteriores de manutenção preventiva.
Etapa 2
É importante conhecer as funções do sistema, incluindo suas entradas e saídas, não importa o quão pequeno seja. Por exemplo: as entradas de uma correia transportadora são as mercadorias e a energia mecânica que alimenta a correia a saída.
Etapa 3
Compreender as diferentes maneiras como o sistema pode falhar. Por exemplo: a correia transportadora pode não transportar as mercadorias com rapidez suficiente ou falhar completamente em transportá-las de uma extremidade à outra.
Etapa 4
O que acontecerá em caso de falha? A falha de ativos pode resultar em preocupações com a segurança e baixo desempenho dos negócios. Também pode afetar outros equipamentos. Os operadores da fábrica, especialistas em equipamentos e técnicos devem trabalhar juntos para identificar as causas-raiz das falhas de ativos individuais. Este processo ajuda a determinar como as tarefas devem ser priorizadas. Pode-se organizar esse processo usando vários métodos, incluindo:
• Análise de efeitos e modos de falha (Failure Mode and Effect Analysis – FMEA): este é um método de avaliação do impacto de uma falha, identificando onde e como um processo pode falhar. Por exemplo: o que faria a correia transportadora desacelerar ou parar de funcionar?
• Análise de falha, modo, efeito e crítica (Failure Mode, Effects and Criticality Analysis -FMECA): o mesmo que FMEA. No entanto, vai além e cria ligações entre os modos de falha, os efeitos e as causas da falha.
• Estudos de perigo e operabilidade (Hazard and Operability Study – HAZOP): é um exame sistemático de processos para identificar problemas que podem resultar em riscos para seu pessoal e ativos. Na maioria dos casos, orienta a revisão dos procedimentos operacionais padrão.
• Análise de árvore de falha (Fault Tree Analysis – FTA): é uma ferramenta gráfica usada para examinar a causa da falha no nível do sistema. Emprega uma análise dedutiva de cima para baixo do fracasso.
• Inspeção baseada em risco (Risk Based Inspection – RBI): é um processo de tomada de decisão usado para otimizar planos de inspeção. É usado principalmente para examinar equipamentos industriais, como tubulações, vasos de pressão e trocadores de calor. No entanto, sempre priorize os modos de falha mais críticos para análise posterior. Retenha os modos de falha que podem ocorrer em um ambiente operacional da vida real.
Etapa 5
Neste ponto, selecionar uma estratégia de manutenção para cada modo de falha crítica, que deve ser econômica e tecnicamente viável. Pode usar manutenção baseada em condição, manutenção preventiva ou manutenção preditiva. Se não conseguir implementar uma determinada estratégia para um modo de falha específico, considere redesenhar o sistema para modificar ou eliminar o modo de falha.
Etapa 6
Implementar a estratégia e realizar revisões regulares: para que o programa MCC seja eficaz, é preciso implementar as recomendações de manutenção identificadas na etapa 5. Após a implementação, as revisões regulares ajudarão a melhorar os sistemas e o desempenho. Qualquer que seja a estratégia de manutenção que decida usar para cada ativo, poderá gerar dados adicionais que irão melhorar seus sistemas.
Por fim, a manutenção centrada na confiabilidade gera ganhos significativos em outras áreas da companhia. Quando se extrapola a análise dos resultados após a implementação da metodologia, é possível notar, em médio e longo prazos:
- Maior confiabilidade
- Maior segurança
- Melhoria na qualidade dos produtos
- Ausência de danos ao meio ambiente
- Maior custo eficaz (quando se assegura, por meio de práticas acertadas de manutenção, que o capital investido tenha o melhor retorno)
Tipos de manutenção
A estratégia para a manutenção centrada em confiabilidade se resume basicamente em cinco tipos de manutenção que, quando combinados, resultam em uma estratégia global de manutenção. Esses tipos são:
Manutenção corretiva
Também chamada de manutenção de avarias, são tarefas executadas para corrigir e reparar sistemas e equipamentos defeituosos. O objetivo é restaurar sistemas que falharam.
Manutenção preventiva
Refere-se à manutenção regular e de rotina para ajudar a manter o equipamento em funcionamento, evitando qualquer tempo de inatividade não planejado e custos caros de falha imprevista do equipamento.
Manutenção preditiva e detectiva
Usa ferramentas e técnicas de análise de dados para detectar anomalias em sua operação e possíveis defeitos em equipamentos e processos para que possa corrigi-los antes que resultem em falha.
Manutenção proativa
É uma estratégia de manutenção preventiva que funciona para corrigir as causas-raiz das falhas e evitar quebras causadas pelas condições subjacentes do equipamento. O objetivo da manutenção proativa é ver as falhas da máquina como algo que pode ser antecipado e eliminado antes que ocorram. A criação de um programa de manutenção proativa ajuda as organizações a encontrar ineficiências ocultas.
Manutenção autônoma
Consiste em uma estratégia de manutenção em que os operadores de máquinas monitoram continuamente seus equipamentos, fazem ajustes e realizam pequenas tarefas de manutenção em suas máquinas. Estas tarefas são realizadas pelo operador, dispensando a utilização de um técnico de manutenção dedicado para realizar a manutenção e manutenção programada regularmente.
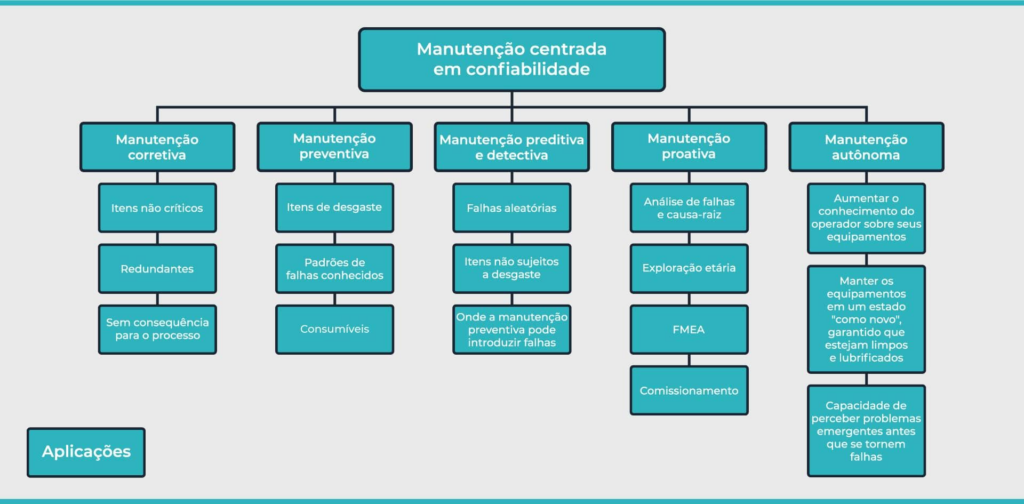
Failure Modes and Effects Analysis (FMEA)
Um dos pontos importantes para a implantação de um programa de MCC – Manutenção Centrada na Confiabilidade – é o FMEA.
FMEA é a sigla de Failure Modes and Effects Analysis, em português: análise dos modos e efeitos de falha.
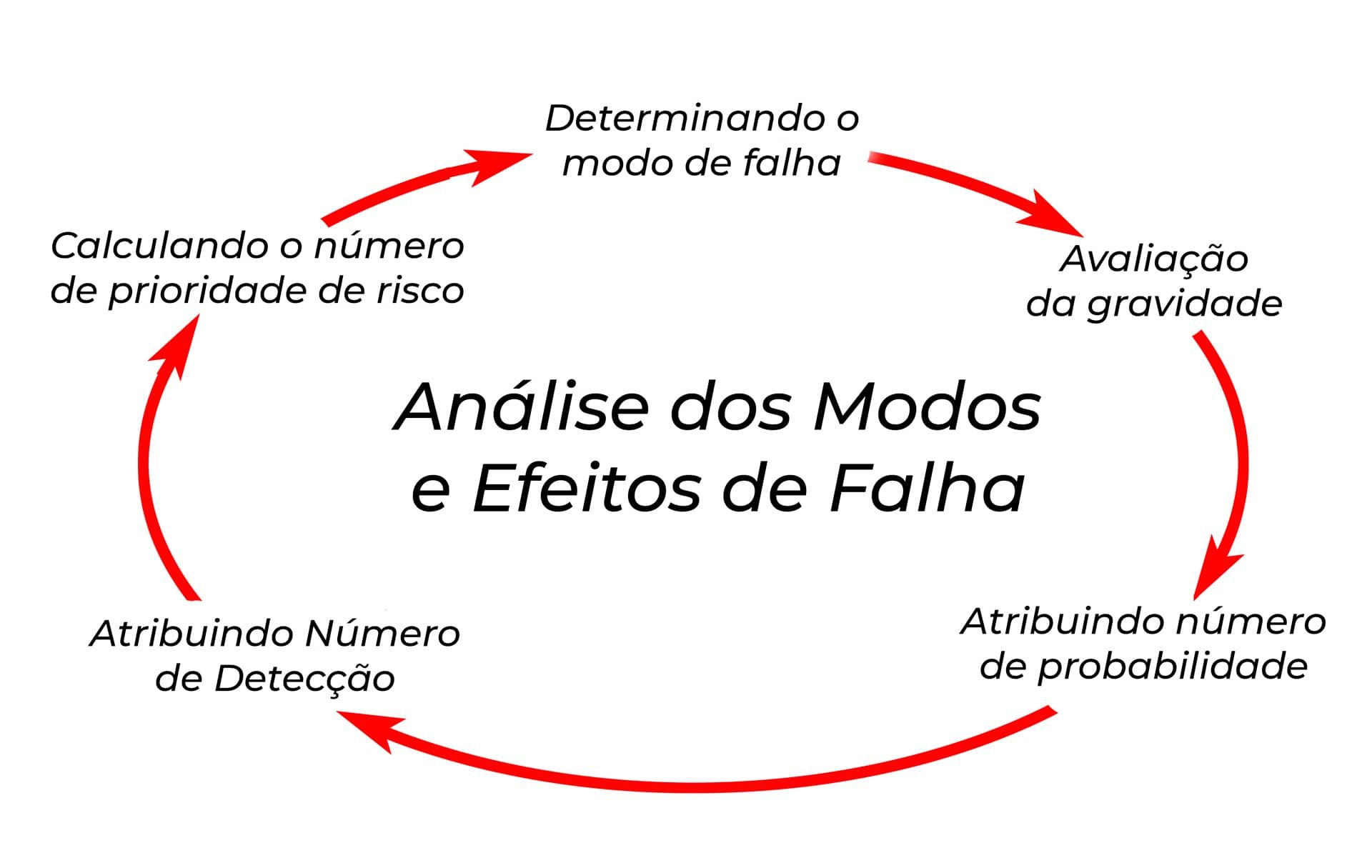
O FMEA consiste na análise do processo produtivo e na verificação das falhas que podem acometer aquele processo, quais são os modos de falha e quais são seus efeitos. A partir desse ponto, elas são pontuadas, sob as óticas de ocorrência, severidade e detecção para o cálculo do número de prioridade de risco (Risk Priority Number – RPN), que nos indicará uma priorização para saná-las.
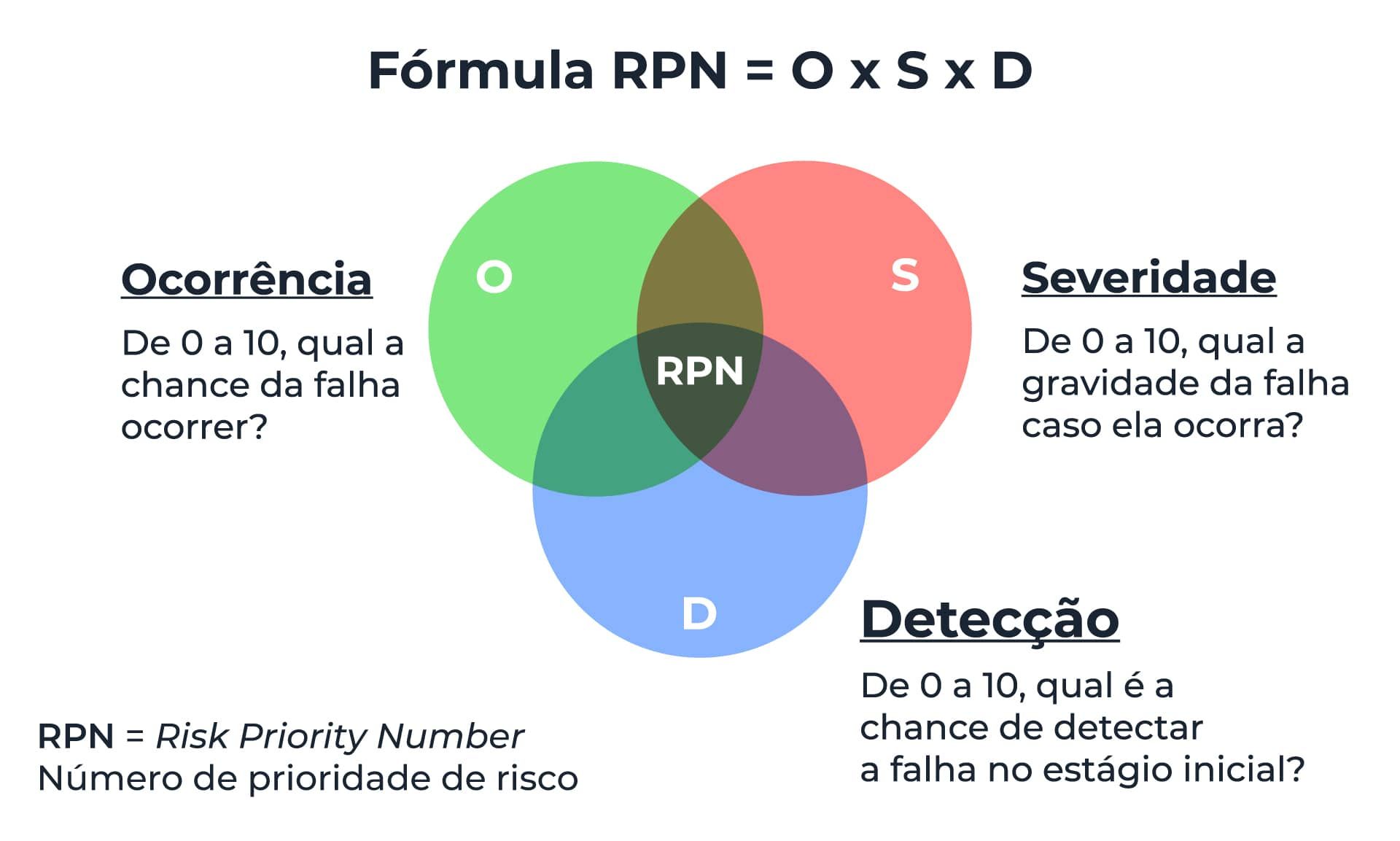
O objetivo do RPN é classificar as falhas de acordo com o risco. Quanto maior for o seu valor, maior é o risco que aquela falha apresenta para o processo e para o negócio, pois mais recursos devem ser aplicados para reduzir esse risco, seja atuando na ocorrência da falha, na severidade ou na detecção.
Usando a ferramenta de análise de efeitos e modos de falha (FMEA), deve-se conduzir uma análise completa de um processo, atribuindo valores numéricos para cada modo de falha de acordo com as instruções e geração um RPN. Recalcule o RPN estimado cada vez que considerar uma mudança no processo, para avaliar o possível impacto da mudança.
Veja na matriz a seguir:
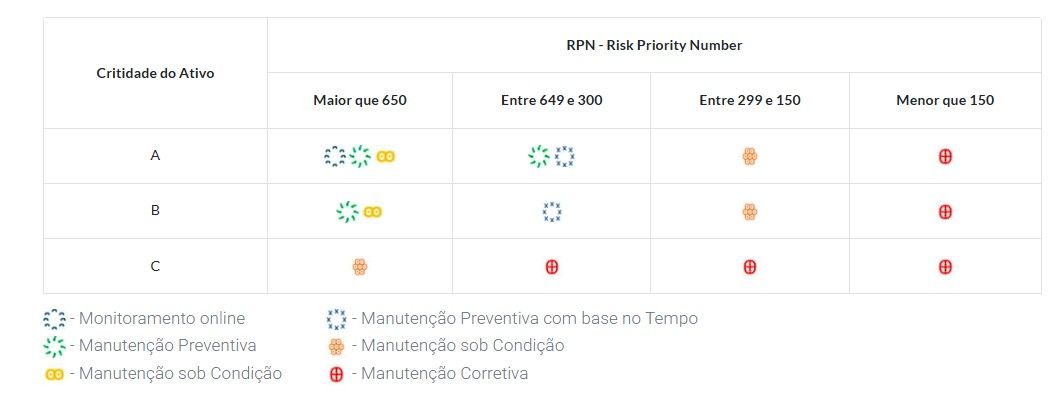
Não necessariamente os números de RPN devem ser iguais aos da matriz.
Junto com a matriz de criticidade, o FMEA irá responder boa parte das perguntas que são mandatórias para uma boa estrutura de RCM:
1. Quais são as funções dos equipamentos que devem ser preservadas?
2. Quais são as falhas funcionais que estão propícias a acontecer?
3. Quais são os modos de falha?
4. Quais são os efeitos de falha?
5. Quais são as possíveis causas de falha?
6. Quais são as consequências severas dessas falhas?
7. Quais são as chances dessas falhas ocorrerem?
8. Quais são as chances de detectar as falhas em estágio inicial?
9. Quais são as ações de manutenção que devem ser aplicadas?
Temos a seguir um exemplo de FMEA:
Ponto da falha | Análise da falha | Avaliação de risco | Ação preventiva recomendada | |||||||
---|---|---|---|---|---|---|---|---|---|---|
Equipamento | Função do Equipamento | Componente | Modos | Efeitos | Causa | Ocorrência | Severidade | Detecção | RPN | |
Redutor de Velocidades Flender – TAG: REDU-63021 | Reduzir a velocidade do acionamento do Elevador de Canecas – TAG ELEV-62145 | Engrenamento | Choque de flancos (vibração excessiva) | Desarme do motor elétrico (para o processo) | Falta de ajuste de backlash | 8 | 9 | 3 | 216 | Inspecionar folga das engrenagens a cada 6 meses. |
Elevação dos níveis de bronze no laudo de análise do óleo | Danificará os rolamentos e demais componentes | Desalinhamento do eixo principal | 7 | 5 | 8 | 280 | Fazer análise de óleo a cada 3 meses. | |||
Rolamentos | Vibração/Temperatura excessivas | Desarme do motor elétrico (para o processo) | Desalinhamento do conjunto motor / redutor | 9 | 8 | 4 | 288 | Fazer análise de vibração mensalmente. | ||
Elevação dos níveis de bronze no laudo de análise do óleo | Desarme do motor elétrico (para o processo) | Falta de lubrificação nos rolamentos | 8 | 8 | 5 | 320 | Lubrificar rolamentos a cada 320 horas. fazer análise de vibração mensalmente. | |||
Retentor de Entrada | Vazamento | Contaminação / perda de lubrificante | Falha na montagem | 9 | 6 | 5 | 270 | Treinamento técnico sobre montagem e manutenção de redutores Flender. | ||
Vazamento | Contaminação / perda de lubrificante | Desalinhamento do conjunto motor / redutor | 9 | 5 | 4 | 180 | Treinamento técnico sobre alinhamento de conjuntos rotativos. Análise de vibração mensalmente. | |||
Retentor de Saída | Vazamento | Contaminação / perda de lubrificante | Falha na montagem | 7 | 8 | 9 | 504 | Treinamento técnico sobre alinhamento de conjuntos rotativos. Análise de vibração mensalmente. | ||
Vazamento | Contaminação / Perda de lubrificante | Desalinhamento do conjunto motor / redutor | 4 | 5 | 8 | 160 | Treinamento técnico sobre alinhamento de conjuntos rotativos. Análise de vibração mensalmente. | |||
Filtro de Ar | Elevação de temperatura | Desarme do motor elétrico (para o processo) | Filtro saturado | 8 | 5 | 4 | 160 | Substituir filtro a cada 320 horas de funcionamento. | ||
Acomplamento | Vibração excessiva | Danificará os rolamentos do motor elétrico / redutor | Falha de lubrificação no acoplamento | 8 | 8 | 7 | 448 | Relubrificar acomplamento a cada 640 horas de funcionamento. | ||
Ruído excessivo | Danificará os rolamentos do motor elétrico / redutor | Desalinhamento do conjunto motor/redutor | 7 | 9 | 10 | 630 | Treinamento técnico sobre alinhamento de conjuntos rotativos. Análise de vibração mensalmente. |
Tabela: Exemplo de FMEA.
Fonte: Autor desconhecido /Site Iqasystem/FMEA RPN, adaptado por Mauro Rezende Filho.
Em um primeiro momento, o FMEA pode ser um pouco complicado, pelo fato de os membros do grupo não estarem familiarizados com a ferramenta, não entenderem as diretrizes do FMEA ou por falta de prática. Por isso, é importante que se treine a identificação de cada item apontado no FMEA, bem como a sua construção.